Offshore wind is growing. Pioneered by countries bordering the North Sea – the UK, Germany and the Netherlands – China now leads the world in offshore wind energy production, with 23.9GW of capacity. The United States has started to take an interest, with President Biden committing to building 30 gigawatts of offshore wind projects by 2030 – which will power more than 10 million homes with clean energy. And Brazil has an ambitious programme to build 72.2GW of capacity, dwarfed only by the UK’s planned additional 78.5GW.
The benefits of offshore wind are clear: higher and more consistent wind speeds, unhampered by mountains or buildings, ensures consistent and high energy output. But the costs are substantial. The harsh marine environment means that the turbines are at far higher risk of damage from corrosion and oxidation. Plus, making repairs is harder, more expensive, and more dangerous than onshore wind. As a result, the cost of offshore wind production is far higher than solar or onshore wind: $133 per MegaWatt hour for floating turbines and $78 for fixed-bottom turbines, compared to $34 per MegaWatt hour for onshore wind (source).
We believe satellite IoT has a role to play in both lowering the cost of production, and improving the safety of workers. Here’s how.
Why is offshore wind production relatively expensive?
A chunky 38% of the operating costs of offshore wind farms is allocated to maintenance. What’s contributing to that cost?
- Equipment failure: on average, each turbine will experience 8.3 failures every year, comprising 6.2 minor repairs, 1.1 major repairs, and 0.3 major replacements
- Manpower: on average, it takes 116 days and 9 technicians to undertake a major replacement, and 7 days and 3 technicians for a minor repair. Delays are frequent, due to ‘no access days’ caused by bad weather
- Ageing equipment: some analysts project that opex costs increase from £184,000 per MegaWatt per year when the turbine is new, to £426,000 per MW/Year when the turbine is 15 years old.
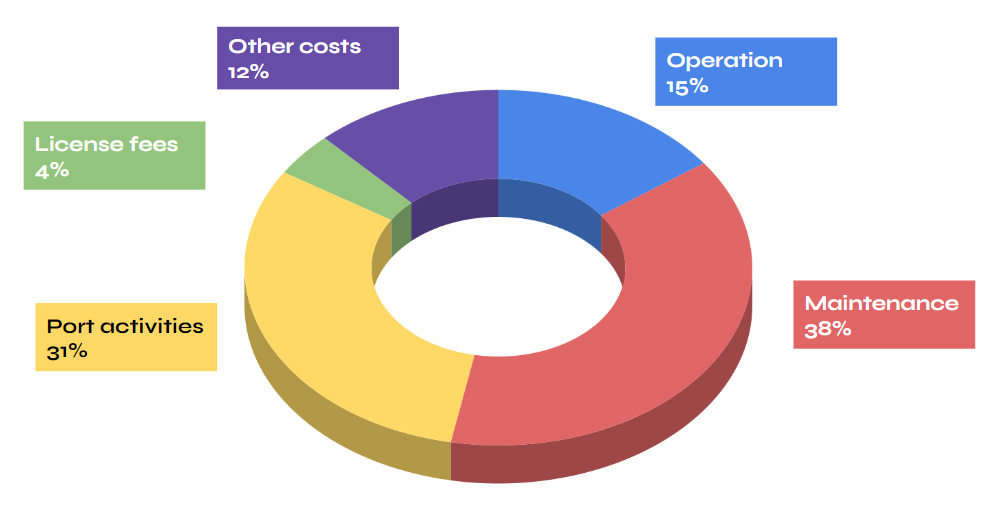
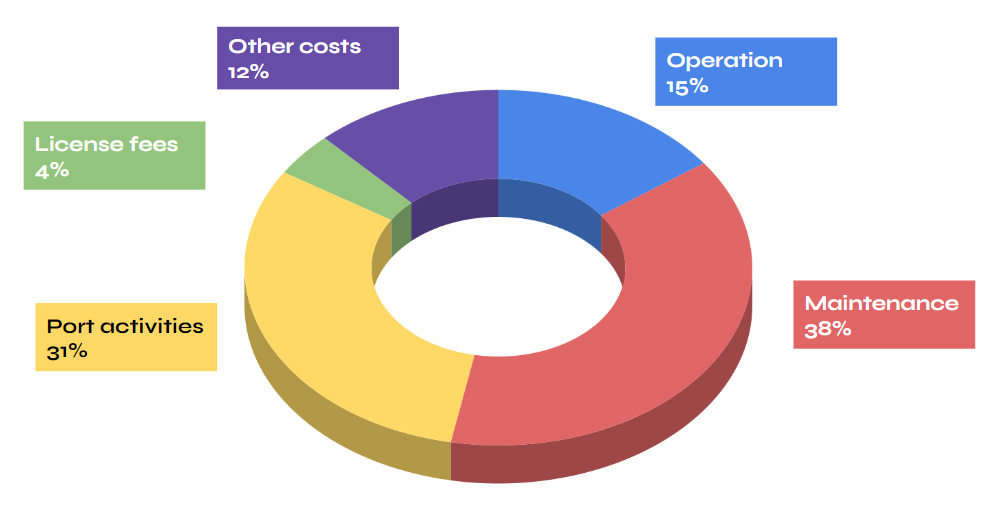
Contact us
What can be done to reduce these costs?
The best answer is predictive maintenance. Supervisory Control and Data Acquisition (SCADA) systems allow operators to monitor and act upon failures or poor performance, and more advanced data collection and analysis allows maintenance tasks to be predicted.
Predictive technologies include Condition Monitoring Systems (CMS). These capture and analyse as much as 250 physical data points, including torque and force measurements, acoustic emissions, electrical strain gauges, oil particle counters and main bearing damage. Sensors capture the data, then AI or machine learning is used to improve the accuracy of the predictions and reduce false alarms as the system is embedded, and the installation base grows.
The benefits for utilising CMS are clear to see, with one monitoring system provider claiming that 90% of developing faults are detected 5 months before failure, driving 175% annual ROI from greater uptime, and reducing emergency maintenance trips by up to 50%.
Predictive maintenance drives 175% annual ROI for offshore wind farms
Further, improving quality control reduces the risk of accidents, which could then reduce insurance premiums.
A key part of this process is the transmission of the sensor data to the cloud, and from there to the client’s IT system, where the data is collected, stored and analysed.
Sensor data is often transmitted through underwater cables, which offers many benefits: it’s fast, secure, and can carry a large amount of data cost-effectively. However wired communication does have drawbacks that can be resolved by co-locating a wireless solution.
Wired vs. wireless or wired plus wireless?
If you already have a wired connection to your wind farm, it’s worth considering a wireless system to complement it, because the ease of adding new sensors to a wireless network is far greater than trying to wire in additional points into a legacy system. You simply need to place your sensors where they need to be to capture the required data, and switch them on. With no need to run cabling, you’re saving time and money, and benefitting from the additional sensor data faster.
Further, because you’re creating a dedicated wireless network for your SCADA data, its findings can be transmitted independently of other data sources. This provides both resilience in the event that your wired connection is disrupted, and allows you, if you choose, to put bespoke security measures around your OT data stream.
In addition to which, you can speed up the rate of data transmission from the industry standard of every 10 minutes, to virtually real time. In turn, this ensures that your maintenance teams get close to real-time information to help inform decisions on what issue to address, when. In fact, Turbit estimates that you can increase output by up to 5% by applying corrective measures faster.
If you were building a new offshore wind farm and decided to use only wireless connectivity to connect your assets, it can cost as little as 10% of the wired alternative, as well as being faster to implement. That said, while the cost of installation is far less, satellite and cellular connections generally come with a monthly usage fee, and they’re only suitable for relatively small amounts of data. For this reason, in our experience, most operators are exploring hybrid wired and wireless setups.
But adding a wireless network isn’t always straightforward for offshore wind farms, as they may fall outside the reach of cellular networks. 4G/LTE services typically extend to around 12 nautical miles from the coast, and wind farms can be built up to 43 miles offshore, which leaves a gap.
That gap can be bridged with a private cellular network, which offers great throughput and tight data security, but this is expensive and time consuming to set up.
Wireless connectivity options for transmitting IoT data from offshore wind farms
LoRaWAN coupled with satellite connectivity is getting an increasing amount of attention for this application. LoRa networks are very easy to set up, and have a wireless range of approximately 16km. They’re specifically designed for IoT data so LoRa-enabled sensors have very long battery lives, but very small data-throughput.
Aggregate each turbine’s sensor data in a LoRaWAN gateway, and then use a single satellite transceiver to transmit the data into the cloud. This is easily achieved with technology that’s widely available today. For example, a device like the RockREMOTE Rugged can be placed almost anywhere on a turbine, as its omni-directional antenna connects with the Iridium satellite network: if the turbine moves, there’s no loss of connection.
This combination of a Wide Area Network and satellite means that most turbines don’t need a specific piece of hardware to communicate to the satellite network: only one, the ‘master’ turbine, needs this, along with the gateway. The gateway can help to lower the cost of data transmission by providing edge computing capabilities: reporting on exception, for example, ensures that only data points falling out of agreed parameters is transmitted.
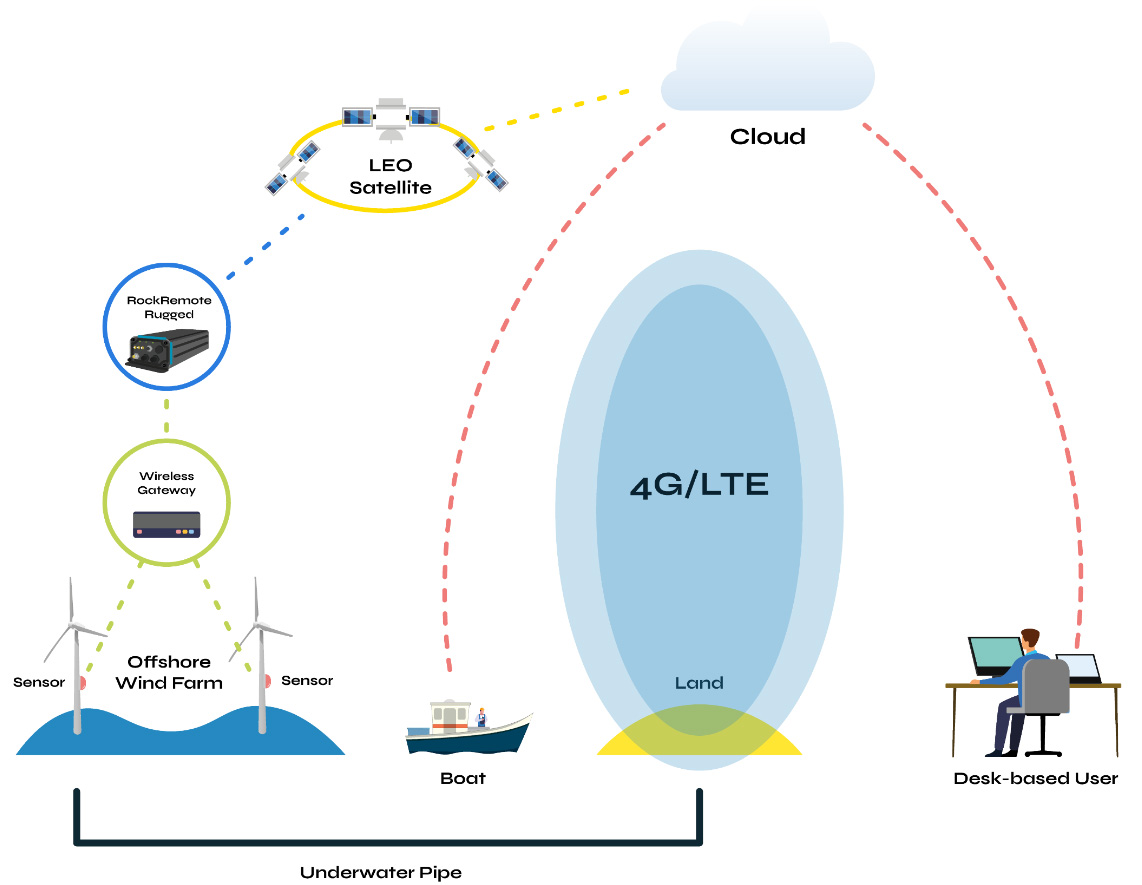
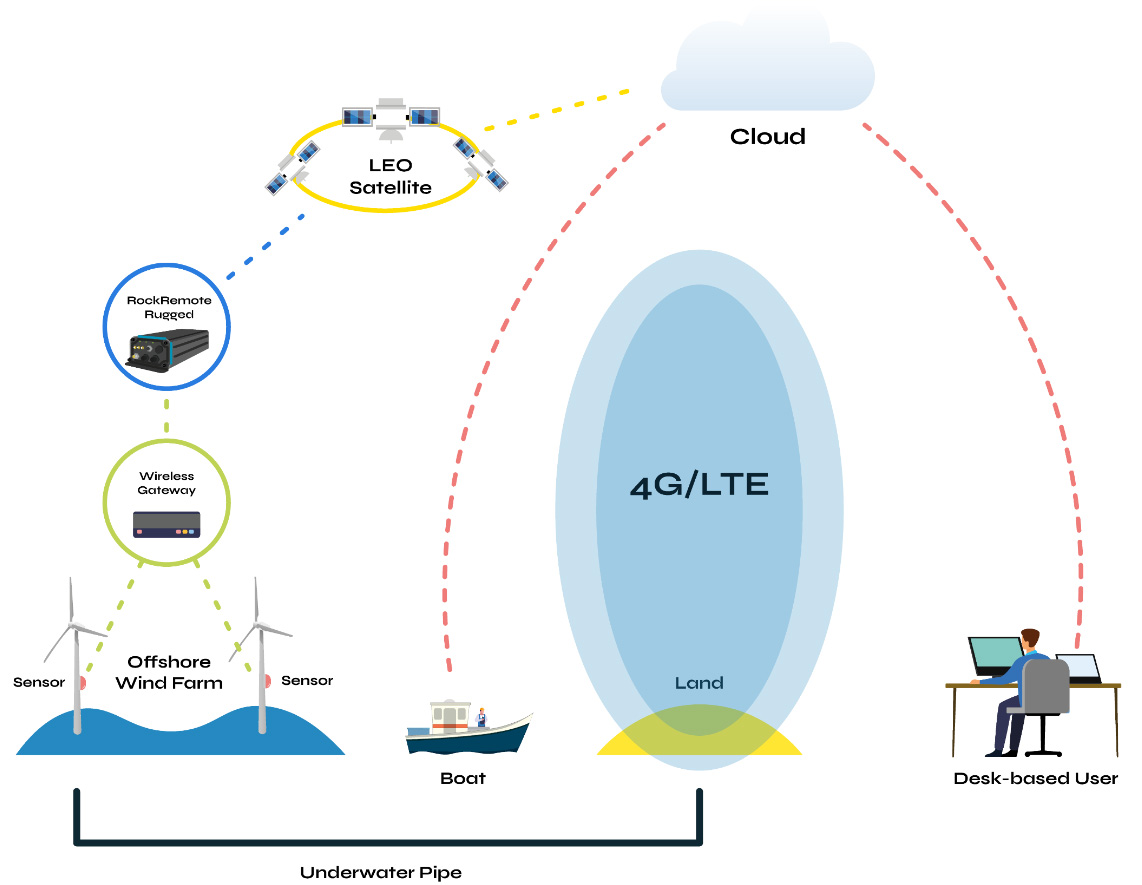
Contact us
Is satellite data transmission expensive?
Because of the recent proliferation of satellite network operators, including Starlink and the soon-to-be-launched Amazon Kuiper Project, the cost of sending your data via satellite has substantially decreased. Existing network operators who have proven their reliability over many years have diversified their product offering to ensure that they can remain competitive with the new entrants (read more about satellite connectivity costs).
As an aside, another great benefit of working with established network operators like Iridium and Inmarsat is that their data transfer mechanisms are trusted by governments and militaries worldwide. As wind farms can be considered critical national infrastructure, and are expected to become more attractive targets for cyber-crime in the near future, knowing that you have access to highly secure data transfer options is very important.
Who else benefits from wireless sensor data transmission?
In addition to the operations team receiving, interpreting and actioning the CMS’ recommendations, another ‘customer’ of wireless sensor data and analysis are the maintenance crews. Frequently located onboard offshore support vessels (OSVs), these people are indispensable for the smooth running of offshore projects.
The same data being captured from sensors and transmitted via satellite to the cloud can also be transmitted to the OSVs. By receiving the data directly, they’ll benefit from being able to effectively triage tasks, without having to wait for instructions from an on-shore team. Real-time wind, humidity, wave height and weather pattern measurements are also essential for maintenance workers’ safety. This sensor data doesn’t need to travel through a fibre connection, as the main requirement comes from the maintenance teams for whom this is critical information.
Recommended OSV satellite IoT hardware
While OSVs usually have a heavyweight VSAT system for crew communication, we’d recommend a separate, lighter-weight system for the transmission of IoT and tracking data, both as a failsafe and to use the bandwidth more efficiently.
The Thales VesseLINK is an ideal for solution for this purpose. It utilises the Iridium satellite network which has 100% global coverage, and the antennas are omni-directional, meaning there’s no need to re-point the device when the OSV moves. Because the network is in Low Earth Orbit (LEO), the latency is low – less than one second. Coupled with the fact that it uses the L-band frequency to transmit data, which is unaffected by weather conditions, Iridium-enabled devices are ideal for mission-critical data.
The Thales VesseLINK is available in two versions: the VesseLINK 200 and VesseLINK 700. The difference between them is the data speeds: the former is designed for IoT data and basic voice / internet access, with data speeds of 176 Kbps. The latter delivers high-speed internet with speeds of 700 Kbps, and creates a WiFi hotspot for any device within a 300 metre range. So it’s capable of far more than transmitting IoT data, but will do so under any conditions.
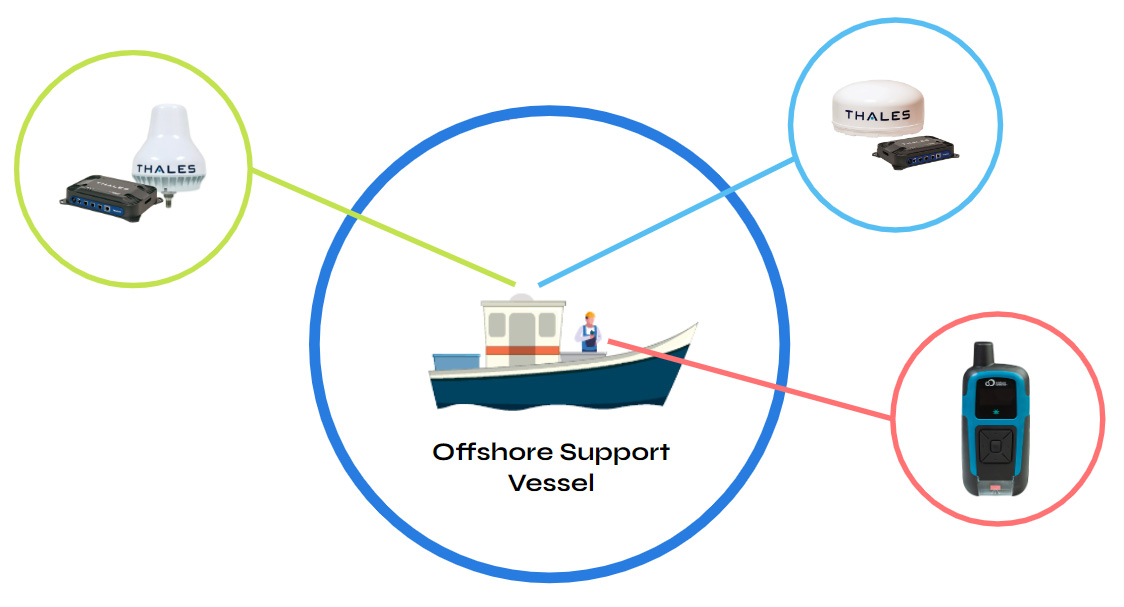
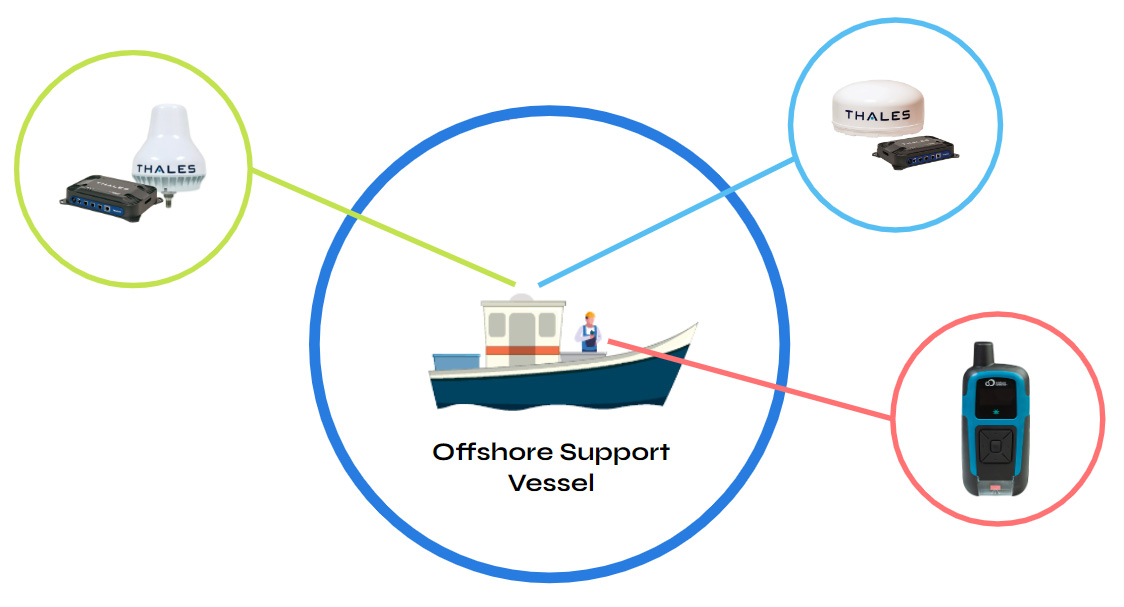
Contact us
Another satellite transceiver we’d suggest exploring is the RockSTAR. This handheld device can connect to wearables sensors like heart rate and body temperature monitors. It also features two-way messaging and an SOS feature. Again using the Iridium satellite network, this data can be transmitted to safety teams to allow for timely inventions, where needed.
Primary, secondary or failover communication
A final note regarding satellite connectivity for your offshore wind farm: it’s highly effective as a back-up communications mechanism should anything happen to your primary means of connecting with the turbines. Underwater cables can be damaged by trawlers, the environment or even malicious intent. With satellite as a back-up, you can still shut down or kickstart your turbines as needed, and communicate with your workers. It’s instant infrastructure that isn’t affected by weather, has no dependency on terrestrial networks, and is highly secure.
Talk to the experts
We can help you make sense of a changing ecosystem and make choices that will continue to deliver for you well into the next decade. Get in touch, and we’ll provide you with objective, expert advice.
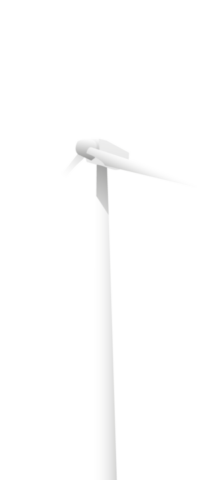
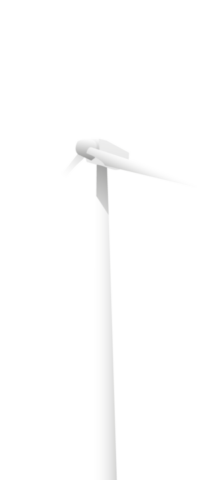